Gas Turbine Flow Meter Common Problems and Quick Solutions
2023-11-27
Gas turbine flowmeter common problems and quick solutions
First, the meter no output
Possible reasons.
1, the power cord is not connected, the voltage is low;
2. The distance between the sensor and the converter of the turbine flowmeter is too far;.
3, the sensor's signal line is broken or poor contact; 4. turbine flowmeter mechanical parts stuck or circuit components are damaged.
Solution.
1, check the power cord to ensure that the power supply voltage is in the specified range meat;
2. Adjust the distance between the sensor and the converter within a reasonable range.
3、Check the signal line of the sensor, rewire or replace the damaged line;
4、Check the mechanical parts and circuit components, repair the damaged parts or replace the new parts.
Second, the meter output is zero
Possible reasons.
1, there is no fluid flowing through the pipe;
2, the sensor and converter connection error;
3, the flow meter sensor is damaged or blocked;
4, the zero drift of the meter is too large.
Solution
1, check whether there is fluid flow in the pipeline to ensure that the fluid is in the flow state
2, check whether the sensor wiring is correct, rewire or replace the damaged line.
3、Check whether the sensor is damaged or blocked, repair the damaged parts or replace the new parts.
4, zero calibration of the meter, adjust the zero drift.
Third, the instantaneous flow fluctuations
Possible causes.
1, the fluid flow is not stable;
2, pipe vibration;
3, the quality of the turbine flowmeter sensor or converter problems.
4, the instrument's parameters are set incorrectly.
Solution.
1, check whether the fluid flow state is stable, if there is an unstable situation, you need to stabilize the fluid flow processing;
2, check whether the pipeline vibration, if there is a vibration problem, need to increase the pipeline support points or vibration damping measures;
3, check the turbine flowmeter sensor and converter whether there is a quality problem, if there is, need to replace the new part of the nature of;.
4、Check whether the parameter setting of the meter is correct, if not, the meter needs to be reset.
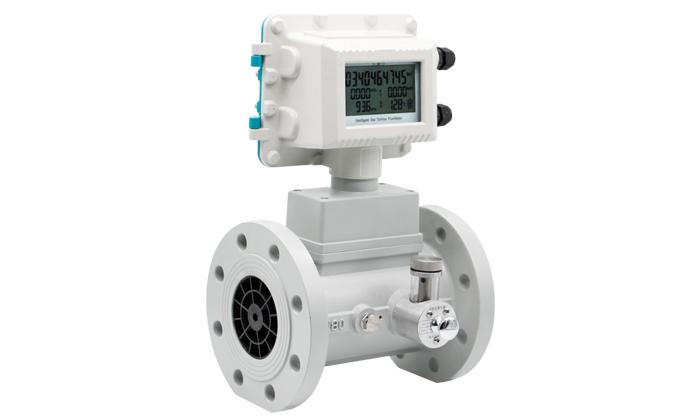
Four, the zero point drift is large
Possible causes.
1, poor contact or broken signal line of the sensor;
2, the mechanical parts of the gas turbine flowmeter wear and tear or circuit components are damaged.
3, the use of the meter environment changes.
First, the meter no output
Possible reasons.
1, the power cord is not connected, the voltage is low;
2. The distance between the sensor and the converter of the turbine flowmeter is too far;.
3, the sensor's signal line is broken or poor contact; 4. turbine flowmeter mechanical parts stuck or circuit components are damaged.
Solution.
1, check the power cord to ensure that the power supply voltage is in the specified range meat;
2. Adjust the distance between the sensor and the converter within a reasonable range.
3、Check the signal line of the sensor, rewire or replace the damaged line;
4、Check the mechanical parts and circuit components, repair the damaged parts or replace the new parts.
Second, the meter output is zero
Possible reasons.
1, there is no fluid flowing through the pipe;
2, the sensor and converter connection error;
3, the flow meter sensor is damaged or blocked;
4, the zero drift of the meter is too large.
Solution
1, check whether there is fluid flow in the pipeline to ensure that the fluid is in the flow state
2, check whether the sensor wiring is correct, rewire or replace the damaged line.
3、Check whether the sensor is damaged or blocked, repair the damaged parts or replace the new parts.
4, zero calibration of the meter, adjust the zero drift.
Third, the instantaneous flow fluctuations
Possible causes.
1, the fluid flow is not stable;
2, pipe vibration;
3, the quality of the turbine flowmeter sensor or converter problems.
4, the instrument's parameters are set incorrectly.
Solution.
1, check whether the fluid flow state is stable, if there is an unstable situation, you need to stabilize the fluid flow processing;
2, check whether the pipeline vibration, if there is a vibration problem, need to increase the pipeline support points or vibration damping measures;
3, check the turbine flowmeter sensor and converter whether there is a quality problem, if there is, need to replace the new part of the nature of;.
4、Check whether the parameter setting of the meter is correct, if not, the meter needs to be reset.
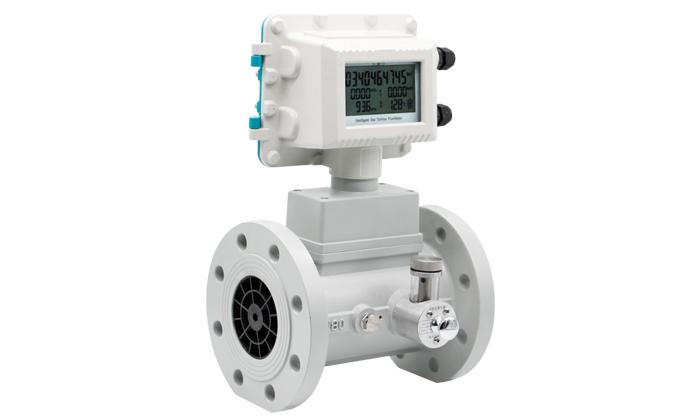
Four, the zero point drift is large
Possible causes.
1, poor contact or broken signal line of the sensor;
2, the mechanical parts of the gas turbine flowmeter wear and tear or circuit components are damaged.
3, the use of the meter environment changes.
Share To:
News
- Why is the thermal gas mass flowmeter not affected by pressure strength and temperature?
- What to do when a thermal gas mass flow meter fails?
- How are thermal gas mass flow meters used? What are the applications?
- Under what circumstances is the gas measurement need to be regulated compensated vortex flowmeter
- Why Is The Aister Thermal Gas Mass Flowmeter So Popular ?
- Gas turbine flowmeter manufacturers explain their main advantages in measurement
- Gas turbine flowmeter manufacturer Aister instrument field experience summary
- Aister Instrument Empowerment Conference